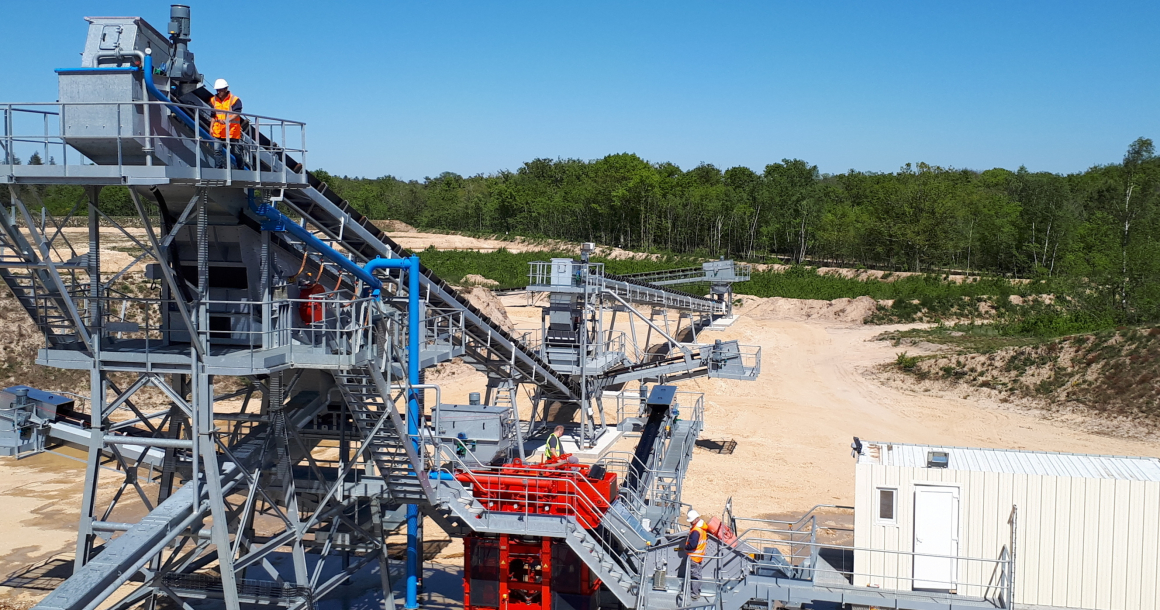
Vue de loin une carrière à tout d’une usine, avec ses charpentes métalliques, ses machines invisibles et le mouvement perpétuel des convoyeurs remplis de roches. Mais pour ce qui est des méthodes, la carrière ne ressemble pas encore tout à fait aux autres manufactures du XXIe siècle. Elle s’en rapproche, petit à petit. L’à-peu-près encore accept...
Continuez votre lecture en créant votre compte et profitez de 5 articles gratuits
Pour lire tous les articles en illimité, abonnez-vous