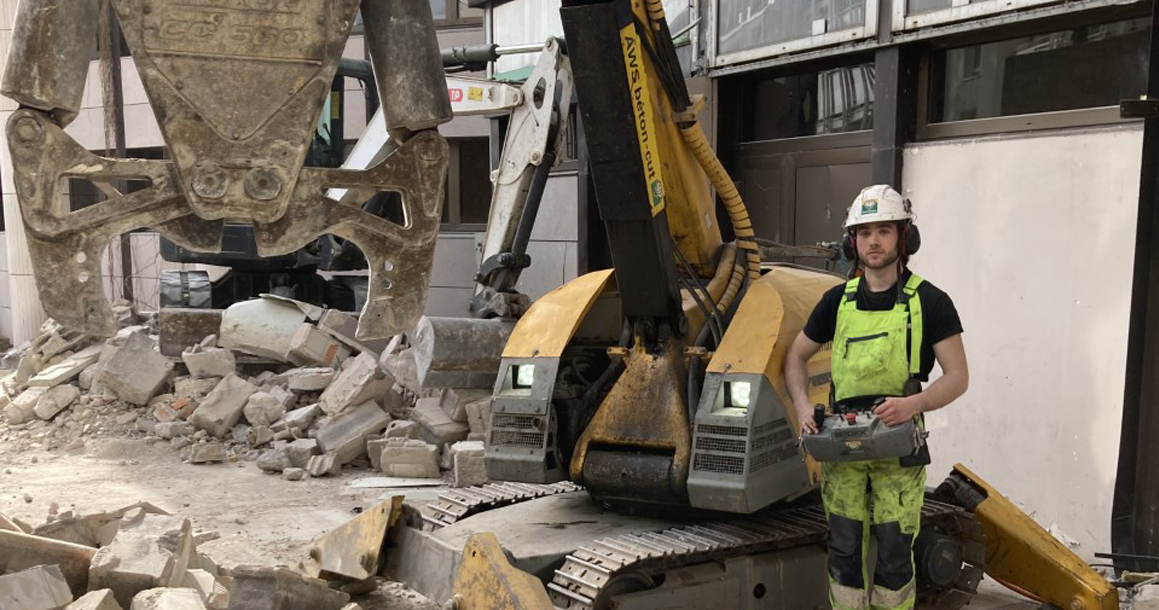
Robots de démolition : attention à ne pas dépasser les limites d’usageEn déclinant de véritables gammes « longues », Brokk et Husqvaran, les deux marques dominant ce matériel de niche, ont sensiblement élargi la palette des applications, tant dans le secteur de la construction, des travaux souterrains, du nucléaire que de l’industrie cimentière e...
Continuez votre lecture en créant votre compte et profitez de 5 articles gratuits
Pour lire tous les articles en illimité, abonnez-vous