Depuis quelques années, toute l'industrie s'intéresse aux possibilités de la fabrication additive. Les constructeurs d'engins de chantier ne font pas exception à la règle. Toutefois, certaines démonstrations peuvent prêter à confusion. Si cette technique se révèle particulièrement adapter pour certaines applications, elle ne peut pas encore répondre seul aux impératifs de la production de masse. (Photo ci-dessous : dans le cadre du projet AME, l'Oak Ridge National Laboratory a réalisé une mini-pelle par impression 3D. © Oak Ridge National Laboratory.) En mars 2017, le salon Conexpo-Con/AGG exposait ses machines rutilantes dans la cours du palais des congrès de Las Vegas. Chaque constructeur y était allé de son engin sensationnel. Dans ce cabinet de curiosités mécaniques, une mini-pelle d’allure quelconque faisait de l’ombre aux mastodontes de métal. En effet, cette dernière était entièrement composée d’éléments créés au moyen d’imprimantes 3D. La prouesse était le fruit du projet de recherche AME, mené par l’Oak Ridge National Laboratory, un institut scientifique américain, associé à plusieurs partenaires dont les groupes Bobcat, Case Construction Equipement et Caterpillar. Ce prototype soulève forcément des interrogations quant au futur de l’industrie. Les lignes de montage spécialisées, symbole de la production de masse, seront-elles remplacées par des outils universels, capables de générer toute sorte de composant en fonction de la demande ? Si ce virage semble probable, il n’en demeure pas moins lointain.
Les défauts de la polyvalence
[caption id="attachment_3604051" align="alignright" width="279"]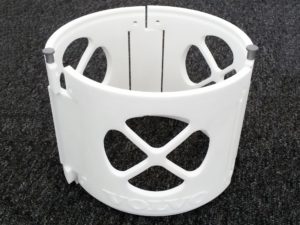
De la chaîne à la chaîne
Malgré ce cahier des charges strictes, les possibilités restent nombreuses. Les pistes évoquées par Volvo et Daimler – les deux groupes du secteur les plus loquaces sur le sujet – donnent un aperçu des débouchés à court terme. L’élaboration de nouveaux outils destinés aux chaînes de montage constitue la première application explorée par les industriels. Du fait de leur géométrie spécifique, les usineurs peuvent mettre plusieurs semaines à les livrer. Avec une imprimante 3D, ce temps est ramené à quelques jours. Elle ouvre même la voie à la conception d’instruments adaptés aux caractéristiques physiques de chaque employé. Les prochains éléments concernés devraient être les petits éléments en plastique intégrés dans les engins, notamment à l’intérieur de la cabine. Il est ainsi possible de proposer des articles sur mesure aux clients. Ce système amène également les entreprises à envisager une production de pièces de rechange à la demande. Volvo Construction Equipement et Mercedes-Benz Trucks étudient la question pour les modèles les plus anciens de leur catalogue. [caption id="attachment_3604050" align="aligncenter" width="600"]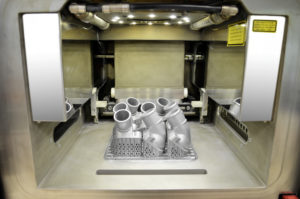
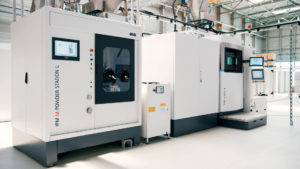