Depuis août dernier, Volvo CE et son client Skanska évalue la faisabilité et la fiabilité du concept d’extraction électrique in situ dans la carrière de Vikan Kross en Suède. Les deux entreprises souhaitait vérifier qu'une production 700 t/h était réalisable. Fin novembre, ils ont révélé les premiers résultats et commenté le premier retour d’expérience.
Le théâtre des opérations est la carrière de calcaire Vikan Kross. Le site, implanté près de Göteborg, est la deuxième plus importante carrière de Skanka, le N°1 suédois de la construction, avec une production journalière de 6 000 t. Exploitée depuis les années 1960, la carrière produit 1,25 millions de tonnes par an de matériaux pour les marchés de la construction et de l’industrie routière. L’objet de cette expérimentation est de tester en conditions réelle la faisabilité de la première carrière à empreinte carbone nulle au monde. Une avancée majeure, qui préfigure le futur de cette filière, moyennant l’électrification de l’ensemble des modes de transport du site, depuis le concasseur primaire, au transport et au concasseur secondaire.
[caption id="attachment_3603305" align="aligncenter" width="600"] La carrière de calcaire Vikan Kross en Suède. (© Volvo CE)[/caption]
En procédant ainsi, les gains d’émissions de carbone sont drastiquement réduits et les coûts totaux d’exploitation abaissés de façon significative. Comme le rappelle Anders Rehnström, président de Skanska Solution Industrial, « nous avons l’ambition d’atteindre la neutralité carbone dans le domaine de la construction, mais cela ne peut se faire seul. Ce partenariat dans le cadre du projet de chantier électrique permet d’avancer dans notre démarche. »
Matériels autonomes
Pour parvenir à ces objectifs, l’ensemble du procédé de la carrière évolue. Les trois tombereaux articulés de 40 t de charge utile sont remplacés par huit modules de transport de matériaux autonomes électriques HX2, de 15 t métrique de capacité d’emport. Au front de taille, une pelle hydraulique biénergie (électrique et thermique) EX1 de 70 t remplace une machine équivalente à moteur thermique traditionnel. Au chargement, une chargeuse LX1 à motorisation hybride électrique alimente les modules de transport. Un concasseur-cribleur électrique a été installé. [caption id="attachment_3603302" align="aligncenter" width="600"]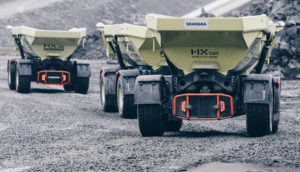
Approche globale
Cette opération expérimentale s’inscrit dans un cadre plus large, le groupe Volvo s’étant engagé dans la lutte contre le réchauffement climatique et ses conséquences. A la fois part du problème mais aussi part de la solution, l’industriel veut passer du discours aux actes. Il veut démontrer que les technologies disponibles peuvent répondre au défi que représente le développement durable en général et la question de l’emprunte carbone en particulier. D’autant plus que Volvo promeut depuis longtemps les notions de durabilité, de sécurité, d’efficacité énergétique et de préservation de l’environnement. En capitalisant sur les expertises des différentes entités du groupe, l’élaboration de cette solution de carrière neutre en carbone a été possible. [caption id="attachment_3603304" align="aligncenter" width="600"]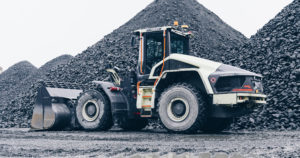
Résultats chiffrés
Pour une production journalière de 6 000 t, l’exploitant réalise une économie de 3 000 l de gazole, le coût énergétique de la carrière étant réduit de 70%. Les conditions de sécurité progressent. Les nuisances liées au bruit et aux émissions, s’estompent. L’environnement de travail s’en trouve amélioré. Le progrès le plus significatif reste la production de CO2 de la carrière : celui-ci est ramené à seulement 166 kg/ jour, contre 8 700 kg/jour auparavant, soit un gain de 98 %, au-delà des objectifs théoriques fixé à 95 %. Le processus nécessitant moins d’opérateur, les gains liés à la main d’œuvre participent aussi à la performance économique de la solution avec un recul de l’ordre de 40 % des coûts liés au personnel. Le coût énergétique diminuant de l’ordre de 70 %, le coût total d’exploitation sont réduits d'environ 25 %. Ainsi, et malgré des coûts d’achat des matériels supérieurs compte tenu des technologies introduites, le retour sur investissement est assuré. Ce premier retour d’expérience met en évidence un besoin de planification prévisionnelle plus précise, condition sine qua non pour programmer une production fluide et constante, dans un cadre organisationnel plus complexe donc plus contraignant. Autre point de vigilance, la fiabilité du réseau Wi-Fi en carrière. En cas de défaillance ou de problème de connexion, la carrière est à l’arrêt. De même, le comportement dans la durée et dans les conditions d’exploitation d’une carrière des batteries qui équipent les modules de transport reste à évaluer dans la durée. Si le système de recharge rapide a démontré son efficacité à l’usage, la tenue des accumulateurs en matière de puissance délivrée et à l’issue de la multiplication des cycles reste à être vérifiée. J-N.O