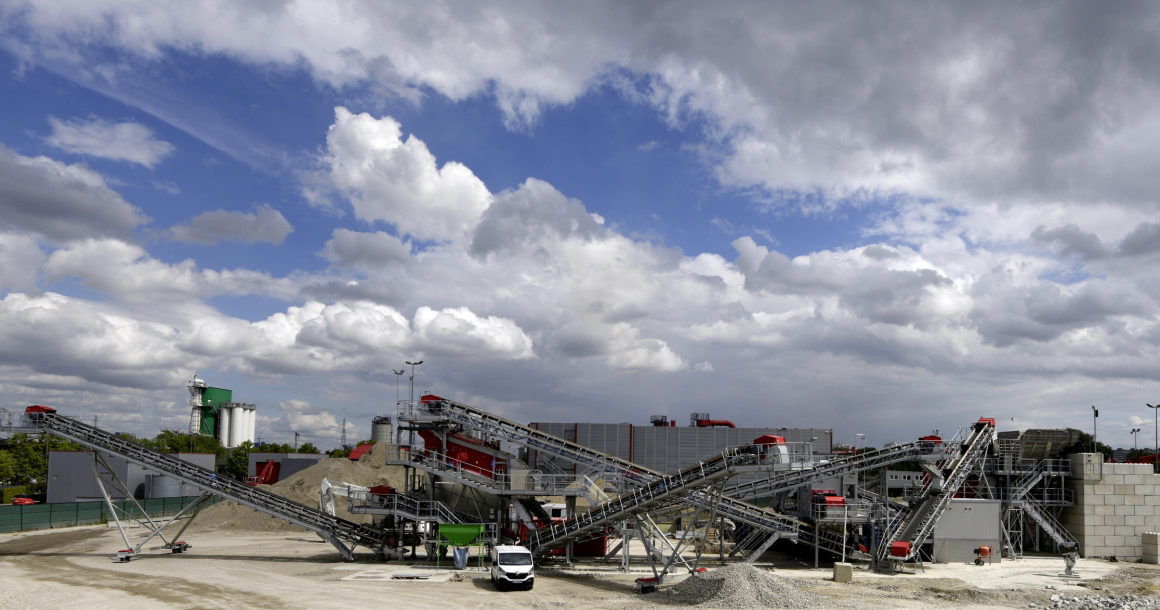
En 2020, quelque 150 000 t de matériaux recyclés ont été consommés sur les chantiers des lignes 14,15, 16 et 18 du Grand Paris. Un tonnage en forte progression qui traduit la montée en puissance de l’économie circulaire et les objectifs de recyclage dans les travaux publics, dans un bassin francilien déficitaire : près de la moitié des granulats pro...
Continuez votre lecture en créant votre compte et profitez de 5 articles gratuits
Pour lire tous les articles en illimité, abonnez-vous