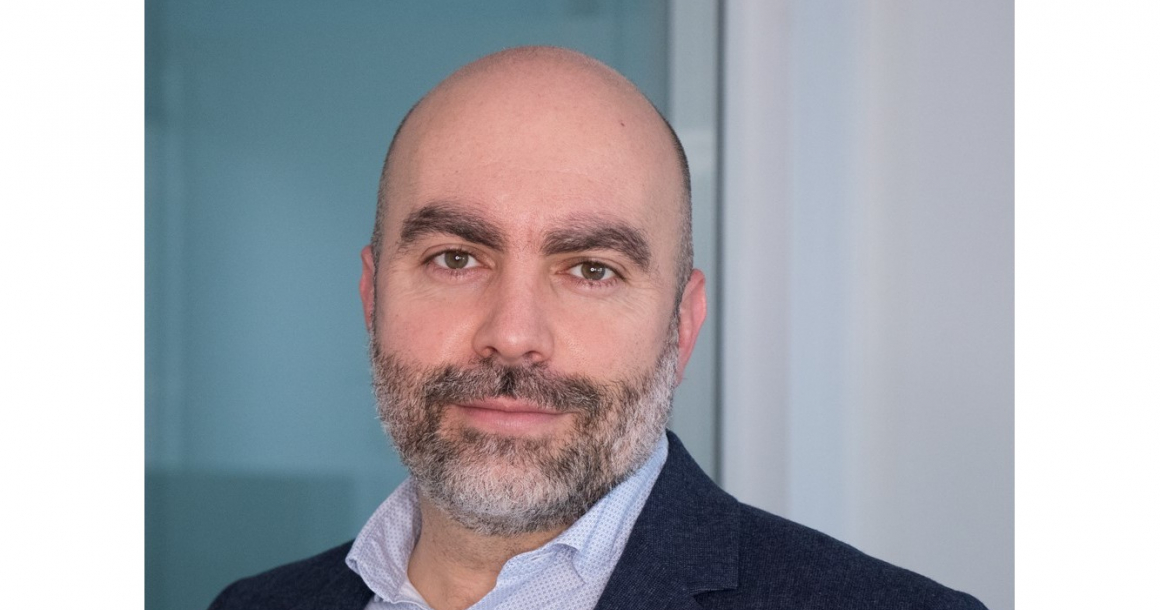
« Nous accompagnons les constructeurs de matériels dans la décarbonation », une interview de Elian Verdier, directeur de la division Mobile chez Bosch Rexroth.Quel est le domaine d’expertise de Bosch Rexroth ?Bosch Rexroth est spécialisé dans le domaine des technologies d’entraînement et de commande, et met en mouvement des machines et systèmes de tou...
Continuez votre lecture en créant votre compte et profitez de 5 articles gratuits
Pour lire tous les articles en illimité, abonnez-vous