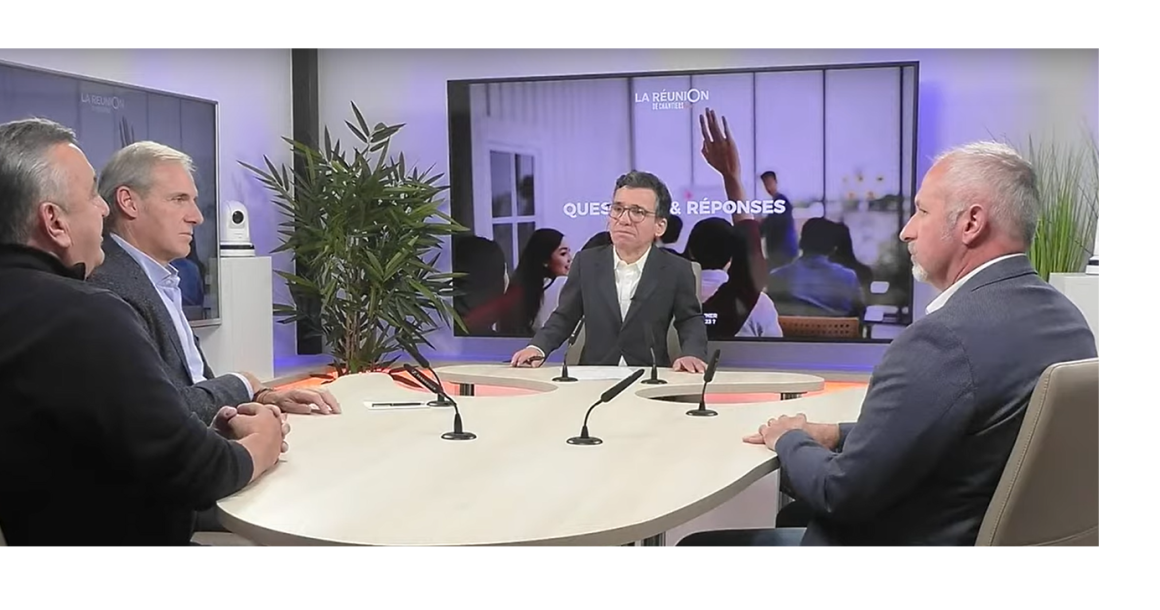
Quelles technologies privilégier pour décarboner son parc ?À la recherche de solutions techniques à même de réduire l’empreinte carbone de leur parc, les directeurs Matériel doivent, dès à présent, procéder à des choix techniques qui les engageront bien au-delà de 2023. Leurs décisions sont d’autant plus difficiles à prendre que les alternativ...
Continuez votre lecture en créant votre compte et profitez de 5 articles gratuits
Pour lire tous les articles en illimité, abonnez-vous